When you drive your car, your mind takes in thousands of data points a second—traffic lights, headlights, distance from the center line, distance to the side of the road, distance between cars, pressure on the brakes, acceleration, sunlight peeking in over the visor, wipers, lights, the song on the radio, what’s in your rearview mirror, signs, buildings, pedestrians, signals, and so on. Thousands and thousands of data points—the details of driving, pouring into your brain every second. Now, imagine putting on a blindfold and getting behind the wheel. Probably not a good idea.
If you did don a blindfold while driving, you wouldn’t know when to turn, what small adjustments needed to be made, or the path for reaching your ultimate destination. Like driving blindfolded, manufacturers who operate without
real-time data and real-time information are asking their operators to run their production lines blindfolded.
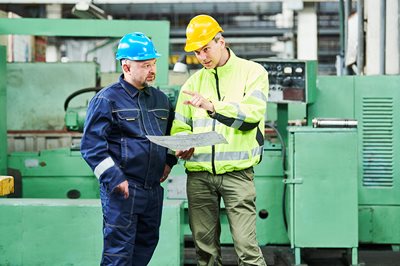
Imagine a manufacturing operator who cannot assess the quality of products being produced, and who has no feedback indicating what adjustments need to be made. Whether blindfolded when driving a car or operating a production line, lack of feedback and information can lead to disaster. Let’s discuss…
Art and Science of Modern-Day Manufacturing
In my opinion, modern-day manufacturing is a mixture of art and science—a very complex endeavor. Companies strive to be as efficient as possible, which means they want to run their production lines at optimal speeds with minimal downtime, so they can get as much product out the door as quickly as possible. The trick is ensuring that you’re creating good quality products while operating at high speed. Doing so is a mix of both art and science.
The art of manufacturing is best understood by operators who have had extensive amounts of time operating a production line. Over time, operators get to know the unique sounds and vibrations—even smells—of the machines they operate. Based upon these inputs, operators understand how each affects the products they are making.
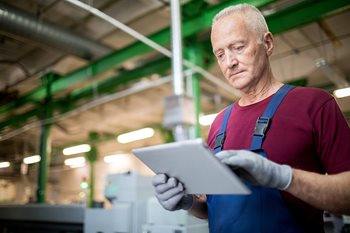
These details form the foundation of what I like to call a machine’s “personality.” When an operator feels a specific vibration combined with a certain scent, it could mean that it’s time to increase conveyor speed, or maybe reduce cooking temperatures. It’s just something that veteran operators intuitively know—because they know the personality of their machine.
Imagine what would happen if these experienced operators could combine real-time data and metrics with their knowledge of machine personality. If so, they would be able to enhance their substantial expertise with raw data and analytics—the essence of manufacturing science. And by combining both art and science, you can supercharge product quality and machine efficiency.
Checks and More Checks…and Operators
In today’s modern manufacturing plants, data is everywhere. Data availability on the shop floor is plentiful—from process-specific temperatures, speeds, and pressures to product quality measurements, machine verifications, and safety checks.
While the frequency of quality checks varies widely, it is important that data be
collected and then analyzed in real-time. This helps provide instantaneous insight into how a machine is running and what is necessary to prevent quality issues. It’s the science to operators’ art, and it can mean the difference between profitably-manufactured items and a shift’s worth of products that gets tossed in the dumpster.
Case in Point
I once worked with a company that manufactured newsprint. Just the paper. Giant rolls of paper. I distinctly remember asking the operator of one of these colossal machines, “What’s really important about the newsprint you make here?”
His response: “The moisture content needs to be just right.” Okay, I thought. That’s interesting… ”How do you know when it’s just right?” He waved me over, and I followed him under the massive machine. A long, wide span of freshly pressed newsprint was flying overhead and re-rolling at the end of the line.
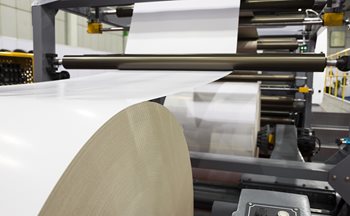
As I walked next to him, the operator placed his forearm over his head, just barely touching the paper that was zipping by. We walked all the way down the length of the machine, the whole time with his forearm just barely touching the newsprint as it continued rolling. When we reached the other side of the machine, he turned to me and reported the newsprint moisture content to within a tenth of a percent.
I was flabbergasted. “How do you know that?” He smiled and calmly said, “I’ve been doing this for 30 years. I know this machine, and I know the moisture content just from the feel of the paper.” Okay, I thought, just taking it in. He continued, “But I know that the moisture content needs to be a couple tenths of a percentage higher.” Now I was smiling right along with him. “And how do you do that?” I asked.
He walked toward the far end again, pointing down. “I turn this knob here, which increases pressure and generates a bit more moisture… but then I’ve got to make sure that it’s applied consistently across the entire web,” he said, referring to the width of the giant roll of paper.
“Once I’ve increased the pressure, I must measure the moisture at several places across the web using a moisture meter. Then I write all that down so I can see how each value changes over time.” In summary, this veteran operator used data analysis together with his artistic expertise to keep his machine running perfectly.
These operators, particularly the ones with years of experience with their machines, know the artistry involved in making sure things run right. And yet this experienced operator
also incorporated the science of data collection and analysis with his artistry—a winning combination for producing high quality products.
No Two Machines Are Alike
What I meant by stating that machines have ”personalities” is that every machine is unique. This is true even though each machine may have “identical” brother and sister machines that are made just like it. Like humans, however, no two machines are exactly alike.
A company I once worked with bought five “identical” milling machines. The only difference between the machines was the serial numbers. The mills were installed on the same shop floor at one of their facilities. Before being approved for production purposes, identical tests were carefully designed and run on each machine for several different material types. What we found was extraordinary.
We found that under the same test conditions, and for the same material types, each machine produced a little different quality from the others. Some machines generated inherently more (or less) product variation than others. One of the mills created dimensions that were just a little larger than the other machines. It was odd for our team to find that five different “quintuplet” machines each ran a little differently. Each mill indeed had its own personality.
But it doesn’t take focused testing to understand a machine’s underlying personality. Operators who run a production line for long periods of time get to know a machine’s quirks, what it likes and what it doesn’t. Operators know from seemingly undetectable sounds and vibrations when a machine is getting tired or a part is wearing out. They know how different vendor products affect a machine. And they know how product quality changes based upon which vendor’s raw materials are being used on the production line.
And yet, even the best operator-artists use real-time data and analyses to further improve quality. They use data to validate that they are, indeed, doing the right things—artistically—with their machines. The data enhances their knowledge of machinery and expands their expertise in running it. The artistry is being scientifically verified by real-time data collection.
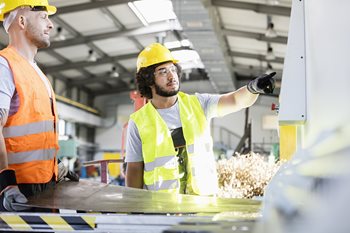
And here’s the beauty of all this: An operator employs his/her art to get their machine humming and working perfectly. But, when they do their next data collection, and the data indicates something has changed, they know that even though they didn’t hear, smell, or feel anything, they need to adjust/fix their machine. Real-time SPC data provides insights they never would have if relying solely on instinct and artistry.
The best operators know that the data they collect expands their knowledge of the machinery and validates their artistry.
Real-time data collection and analysis in manufacturing is the merging of art and science. We give the artists even more information they can use to make real-time adjustments and improvements to their machines—so they can improve their ability to prevent off-quality product from being manufactured.
Okay, I Can’t Clone My Operators—What Do I Do?
Maybe you can’t clone those magnificent, experienced operator-artists, but you can clone their
best practices. What they do correctly can be communicated to other operators with standard operating procedures (SOPs). Find out best practices from the most experienced operators—from both the artistry and data perspectives—capture that information and share it with the staff.
Standard operating procedures help communicate the art of successfully running a production line. SOPs also enable companies to minimize reliance on pure artistry. You don’t want to do away with it, obviously, because (as we’ve discussed) that artistry is valuable.
When less experienced operators use SOPs, there’s only so much they can understand about the art of running a production line. And that’s when real-time data collection and analysis is a boon to these newbies. Making machines run right and ensuring the manufacture of high-quality products is significantly enhanced through the reliance on real-time data, and the insights they provide to both rookie and veteran operators.
In Closing
So, all that data coming in—the sounds the machine is making, the temperatures, the humidity, the moisture, the speeds, all of it—is the inspiration for operator-artists to adjust, tweak, and care for their machines. But it can take decades to become a true production line Picasso—time most organizations don’t have.
To expedite process control information and minimize quality issues, companies need to capitalize on real-time data collection and analysis. Doing so enhances the expertise and artistry of veteran operators while accelerating rookie operators’ expertise. And lastly, real-time data provides instantaneous insights and information to all operators, ensuring your organization won’t be driving their machinery blindfolded.
Take advantage of the technology at your fingertips today: contact one of our account managers (1.800.772.7978 or
via our website) for more information.